Troubleshooting and Response Strategies for Centrifugal Fans: Authoritative Guide!
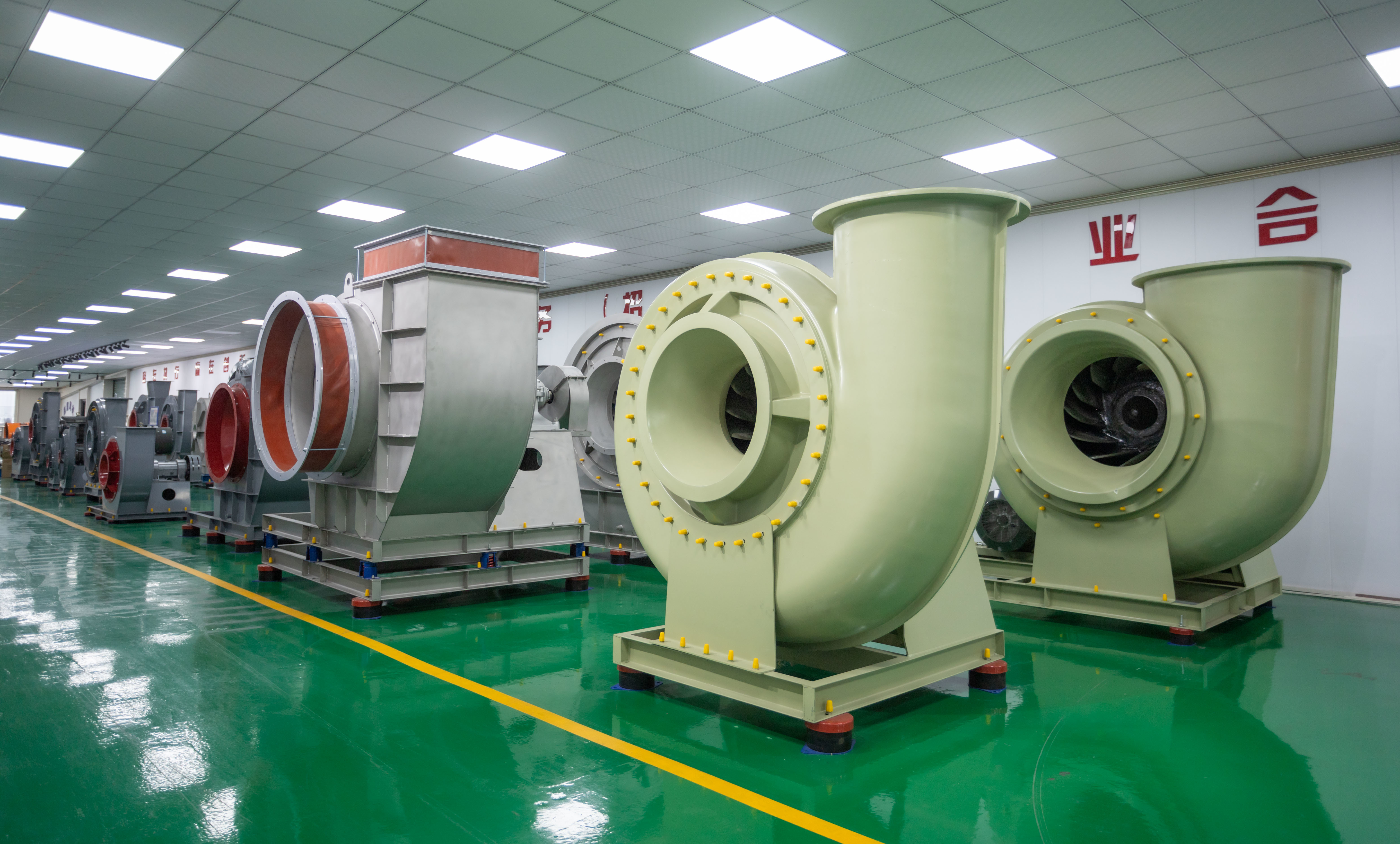
Centrifugal fans are essential components in various industrial and commercial applications, providing crucial airflow for ventilation, cooling, and exhaust systems. However, like any mechanical equipment, they can encounter issues that affect their performance. This guide aims to provide a comprehensive overview of troubleshooting techniques and response strategies for centrifugal fans, ensuring optimal operation and longevity.
Understanding the Basics of Centrifugal Fans
Before diving into troubleshooting, it is vital to understand how centrifugal fans operate. These fans use a rotating impeller to increase the velocity of air, converting kinetic energy into pressure energy. The design typically includes a housing that directs airflow, making them suitable for various applications. Familiarity with the basic components—such as the impeller, motor, bearings, and housing—will aid in identifying potential issues.
Common Issues with Centrifugal Fans
Centrifugal fans may experience a range of problems, including:
1. Vibration:Excessive vibration can indicate an imbalance in the impeller or misalignment of the motor.
2. Noise: Unusual sounds may signal issues such as worn bearings or airflow obstructions.
3. Reduced Airflow:This can result from a clogged filter, duct obstructions, or impeller damage.
4. Overheating:Overheating may be caused by motor overload, insufficient airflow, or lubrication failure.
5. Electrical Failures:Problems with the motor or power supply can lead to fan failure.
Step-by-Step Troubleshooting Process
When encountering issues with a centrifugal fan, a systematic troubleshooting approach is essential. Follow these steps:
1. Identify the Symptoms:Begin by observing the fan's performance. Note any unusual sounds, vibrations, or changes in airflow. Documenting these symptoms will help in diagnosis.
2. Inspect the Fan:Conduct a visual inspection of the fan and its components. Look for signs of wear, misalignment, or obstructions. Check for dirt buildup on the impeller and housing, as this can impede airflow.
3. Check Electrical Components: Examine the electrical connections, ensuring that the power supply is stable and that there are no loose wires. Use a multimeter to test the voltage and current supplied to the motor.
4. Assess the Bearings: Worn or damaged bearings can cause excessive vibration and noise. Rotate the fan by hand to feel for roughness or binding, which may indicate bearing failure.
5. Evaluate the Ductwork: Inspect the duct system for blockages or restrictions. Ensure that filters are clean and that there are no sharp bends that could hinder airflow.
6. Test the Motor:If the fan is not operating, test the motor for functionality. Check for overheating or any unusual smells that could indicate electrical failure.
Response Strategies for Common Issues
Once the problem has been identified, appropriate response strategies can be implemented:
1. Addressing Vibration:If vibration is detected, check for imbalance by inspecting the impeller and ensuring it is clean and free from debris. Realign the motor if necessary and replace any worn bearings.
2. Mitigating Noise: To reduce noise, lubricate bearings and ensure all components are securely fastened. If noise persists, consider replacing worn parts or adding vibration dampeners.
3. Restoring Airflow:Clear any obstructions in the ductwork and replace clogged filters. If the impeller is damaged, it may need to be repaired or replaced to restore proper airflow.
4. Preventing Overheating: Ensure the fan is not overloaded by checking the system design and airflow requirements. Improve ventilation around the motor and regularly lubricate bearings to prevent overheating.
5. Resolving Electrical Failures:If electrical issues are identified, repair or replace damaged wiring. Ensure the motor is compatible with the power supply to avoid future failures.
Preventive Maintenance Strategies
To minimize the risk of issues arising in the first place, implement a regular maintenance schedule. Key preventive measures include:
1. Regular Inspections:Conduct routine inspections to identify wear and tear before it leads to failure. Check for dirt buildup and clean components as needed.
2. Lubrication:Ensure bearings are adequately lubricated according to manufacturer specifications. Regular lubrication can significantly extend the lifespan of the fan.
3. Balancing:Periodically balance the impeller to prevent vibration and wear. This is especially important after maintenance or repairs.
4. System Audits:Regularly assess the entire airflow system to ensure it operates efficiently. Look for areas that may need upgrading or modification.
5. Training Personnel: Ensure that staff operating and maintaining centrifugal fans are adequately trained. Knowledgeable personnel can spot potential issues early and respond appropriately.
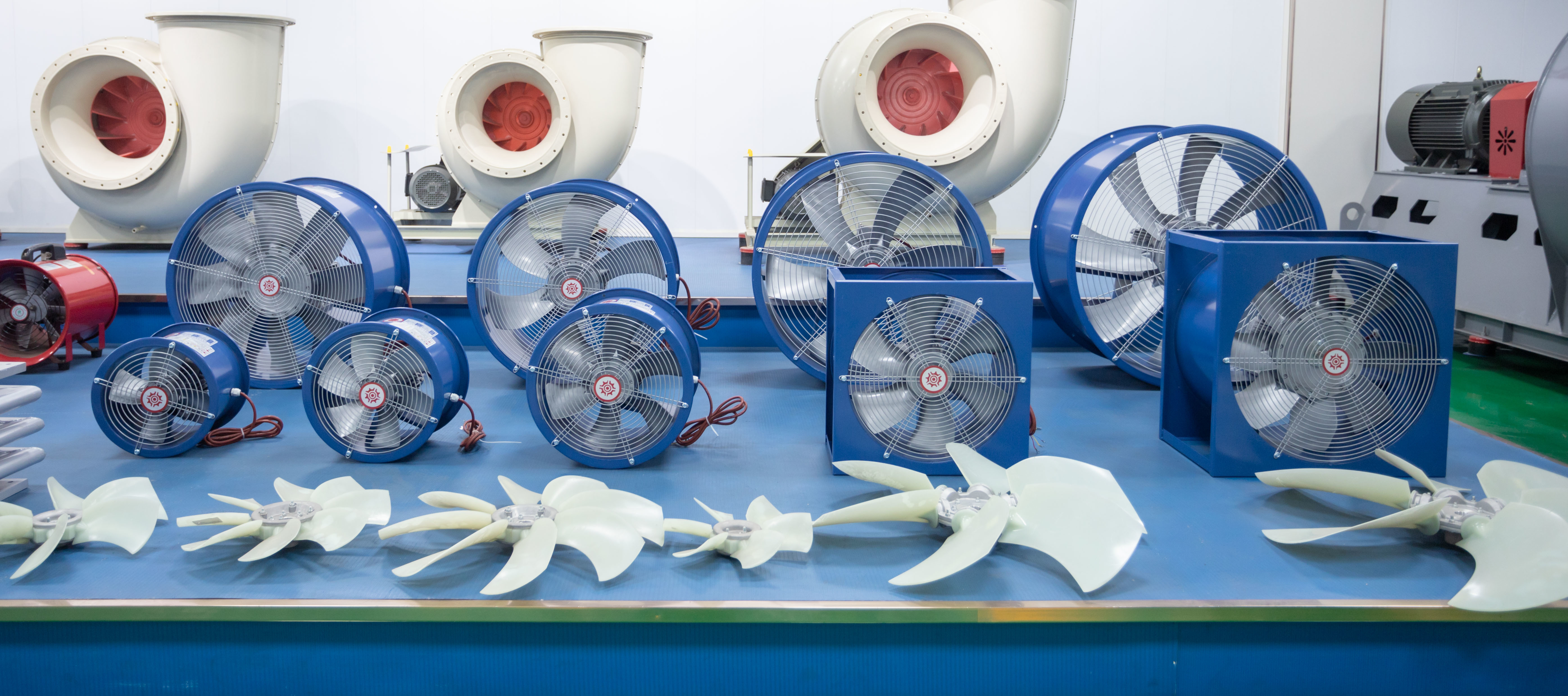
Conclusion
Centrifugal fans are critical to many industrial processes, and understanding how to troubleshoot and respond to issues is essential for maintaining their performance. By following a systematic troubleshooting process and implementing preventive maintenance strategies, facility managers can ensure the longevity and efficiency of their centrifugal fans. Remember, proactive maintenance is always more cost-effective than reactive repairs, so invest the time and resources necessary to keep your systems running smoothly.
Tag:
Recommend News